Automação Industrial: integrando sistemas elétricos com PLCs
A automação industrial tem sido um divisor de águas na maneira como as indústrias operam, trazendo eficiência, precisão e confiabilidade para os processos produtivos.
Para isto, Controladores Lógicos Programáveis (PLCs) agem como cérebros do processo, dispositivos eletrônicos que gerenciam e controlam máquinas e processos industriais.
A integração de sistemas elétricos com PLCs não é apenas uma prática moderna; é uma estratégia essencial que permite às indústrias alcançar um nível superior de automação.
O que é um PLC?
São dispositivos robustos e versáteis são projetados para realizar controle automático de máquinas e processos, interpretando dados de entrada de sensores e atuando sobre dispositivos de saída para executar ações específicas.
Leia também
- Principais normas elétricas utilizadas pelos eletricistas!
- Cabo de rede: qual o certo para o seu computador?
Arquitetura de um PLC
A arquitetura de um PLC pode ser dividida em várias partes essenciais:
CPU (Unidade Central de Processamento): É o coração do PLC, responsável pelo processamento de programas, cálculos, lógica de controle, e gerenciamento de tarefas e comunicações. Ela executa o software do sistema e as aplicações carregadas pelo usuário.
Memória: Armazena o programa do usuário e os dados necessários para a operação, incluindo variáveis, temporizadores, contadores e configurações de hardware. A memória pode ser volátil ou não volátil, garantindo que os programas e dados sejam preservados durante desligamentos.
Módulos de Entrada/Saída (E/S): Conectam o PLC com o mundo externo, recebendo sinais de sensores (entradas) e enviando comandos para atuadores (saídas). Esses módulos podem ser digitais, para sinais on/off, ou analógicos, para sinais que variam continuamente.
Fonte de alimentação: Fornece energia elétrica para o funcionamento do PLC e, em alguns casos, para os sensores e atuadores conectados ao sistema.
Interfaces de comunicação: Permitem a comunicação do PLC com outros dispositivos de controle, sistemas de supervisão, redes industriais e interfaces homem-máquina (IHM), facilitando a integração e o gerenciamento de dados.
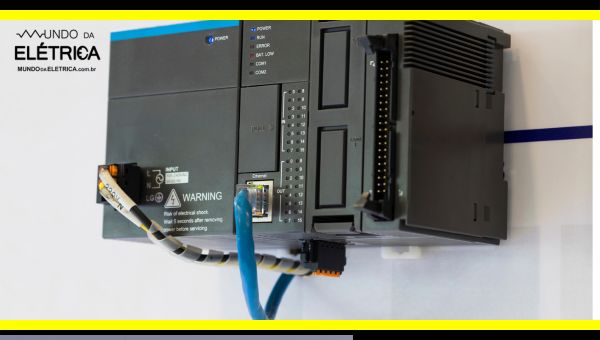
Uma forma de programar máquinas, o PLC ajuda a manter indústrias em pleno funcionamento, dentro de uma máxima capacidade. (Imagem: Equipe)
Como funciona um PLC?
O funcionamento de um PLC baseia-se em ciclos de varredura, que consistem em três etapas principais:
Leitura de Entradas: No início de cada ciclo, o PLC lê o estado atual de todas as entradas conectadas e armazena esses dados em sua memória.
Execução do Programa: Com base nas entradas, o PLC executa o programa de controle carregado na memória, aplicando a lógica de controle para determinar as ações a serem tomadas. Este programa pode incluir instruções de lógica, sequenciamento, temporização, contagem e operações matemáticas.
Atualização das Saídas: Após a execução do programa, o PLC atualiza as saídas, enviando comandos aos dispositivos de saída com base nos resultados do programa.
Componentes em um sistema de automação industrial que usa um PLC
Os sistemas de automação industrial com Controladores Lógicos Programáveis (PLCs) são compostos por diversos componentes interconectados que trabalham em conjunto para executar operações complexas de forma eficiente e confiável. .
1. Controlador Lógico Programável (PLC)
O PLC é o coração do sistema de automação, responsável por executar o software de controle que processa as entradas e determina as saídas. Ele é programado para realizar uma ampla gama de funções lógicas, sequenciais, temporizadas e aritméticas, com base nas informações recebidas dos sensores e outros dispositivos de entrada.
Os PLCs são projetados para operar em ambientes industriais adversos, oferecendo robustez, flexibilidade e capacidade de expansão.
2. Sensores e dispositivos de entrada
Os sensores são utilizados para coletar dados do ambiente ou do processo industrial, como temperatura, pressão, nível de líquido, posição e velocidade.
Esses dados são enviados ao PLC, que os utiliza para tomar decisões de controle. Os dispositivos de entrada também incluem botões, chaves e outros mecanismos que permitem a interação humana com o sistema.
3. Atuadores e dispositivos de saída
Os atuadores são os componentes que realizam a ação física no sistema, como motores, válvulas, solenoides e cilindros pneumáticos ou hidráulicos.
Eles são controlados pelo PLC, que ativa ou desativa esses dispositivos com base na lógica de programação para alterar o estado do processo ou do sistema. Dispositivos de saída também podem incluir indicadores luminosos, alarmes e outros elementos de sinalização.
4. Interfaces homem-máquina (IHM)
As IHMs permitem a interação entre os operadores humanos e o sistema de automação. Elas exibem informações sobre o estado do sistema, alarmes e dados históricos, além de permitir que os operadores modifiquem parâmetros do processo, iniciem ou interrompam operações e visualizem diagnósticos do sistema.
As IHMs variam desde simples displays e painéis de botões até sofisticadas telas sensíveis ao toque com interfaces gráficas avançadas.
5. Módulos de comunicação
Os módulos de comunicação possibilitam a troca de dados entre o PLC e outros sistemas, dispositivos ou redes industriais.
Isso inclui a comunicação com outros PLCs, computadores de supervisão e controle, sistemas de gestão empresarial (ERP) e dispositivos de campo inteligentes. Esses módulos suportam diversos protocolos de comunicação industrial, como Modbus, Profibus, Ethernet/IP e outros, facilitando a integração do sistema.
6. Fonte de alimentação
A fonte de alimentação é essencial para fornecer energia elétrica estável e segura para o PLC e outros componentes do sistema. Ela deve ser capaz de suportar as variações de carga e garantir a continuidade operacional, mesmo em condições adversas ou em caso de falhas na rede elétrica.
7. Dispositivos de segurança
Os dispositivos de segurança são cruciais para proteger o sistema, os dados e, principalmente, os operadores e técnicos que interagem com a automação. Isso inclui relés de segurança, cortinas de luz, botões de emergência e sistemas de parada de emergência (E-stop), que garantem uma parada segura do processo ou da máquina em caso de situações de risco.
Como é a integração de sistemas elétricos com PLCs?
A integração de sistemas elétricos com Controladores Lógicos Programáveis (PLCs) é um processo que envolve a conexão e comunicação entre os componentes elétricos de uma máquina ou processo industrial e um PLC, que atua como o cérebro do sistema de automação.
Essa integração permite que as operações industriais sejam automatizadas, monitoradas e controladas de maneira eficiente e precisa.
1. Planejamento e análise
O primeiro passo na integração de sistemas elétricos com PLCs envolve um planejamento detalhado e análise das necessidades do sistema. Isso inclui entender os processos que precisam ser automatizados, os requisitos operacionais, as especificações técnicas dos dispositivos elétricos e as condições ambientais do local.
Com base nessa análise, selecionam-se os componentes adequados, incluindo o tipo de PLC, módulos de entrada/saída (I/O), sensores, atuadores e dispositivos de comunicação.
2. Escolha do PLC e configuração dos módulos I/O
A escolha do PLC adequado é crítica, considerando-se a complexidade do sistema, o número de entradas e saídas necessárias, a velocidade de processamento e as capacidades de comunicação.
Os módulos de entrada coletam sinais de dispositivos de campo, como sensores, enquanto os módulos de saída enviam sinais para ativar atuadores, como motores e válvulas. Esses módulos devem ser configurados adequadamente para se comunicar com os dispositivos elétricos específicos utilizados no sistema.
3. Desenvolvimento do software de controle
O próximo passo é o desenvolvimento do software de controle que será carregado no PLC. Esse software define a lógica de controle do sistema, incluindo o processamento de sinais de entrada, a tomada de decisões lógicas e a ativação de dispositivos de saída.
A programação do PLC pode ser realizada em várias linguagens, como Ladder, Blocos de Funções ou Texto Estruturado, dependendo das preferências do desenvolvedor e das capacidades do PLC.
4. Integração e conexão física
Após a seleção e configuração dos componentes e o desenvolvimento do software, procede-se à integração física e à conexão dos dispositivos elétricos ao PLC. Isso inclui a instalação de cabos, a conexão de sensores e atuadores aos módulos de entrada e saída, e a configuração dos sistemas de comunicação.
Durante essa fase, é crucial seguir as melhores práticas de instalação elétrica e garantir a segurança operacional do sistema.
5. Testes e ajustes
Antes da operação completa, o sistema integrado passa por uma série de testes para verificar a funcionalidade e a precisão da automação. Isso inclui testar a comunicação entre o PLC e os dispositivos de campo, a execução correta da lógica de controle e a resposta dos atuadores.
Ajustes e otimizações podem ser necessários para garantir que o sistema atenda às especificações e aos requisitos operacionais.
6. Monitoramento e manutenção
Após a integração e a entrada em operação, o sistema precisa ser monitorado continuamente para garantir seu desempenho ótimo. Isso pode incluir o monitoramento remoto através de Interfaces Homem-Máquina (IHMs) e sistemas de supervisão e aquisição de dados (SCADA).
A manutenção preventiva e as atualizações regulares do software também são essenciais para manter a eficiência e a segurança do sistema.
Exemplos de aplicações para os PLCs
Os Controladores Lógicos Programáveis (PLCs) são extremamente versáteis e encontram aplicações em uma vasta gama de indústrias, desde a manufatura até serviços de utilidade pública, passando por controle de processos e sistemas de automação predial.
Eles são projetados para realizar controle automático de processos, monitoramento de máquinas e execução de tarefas específicas com alta confiabilidade e precisão.
1. Manufatura
Linhas de montagem: Os PLCs controlam as operações sequenciais em linhas de montagem automatizadas, como a montagem de automóveis, garantindo a sincronização e a precisão dos processos.
Controle de máquinas CNC: Na fabricação de peças mecânicas, os PLCs são usados para controlar máquinas-ferramenta CNC (Controle Numérico Computadorizado), gerenciando operações de corte, furação e fresagem.
2. Embalagem
Sistemas de enchimento: Em indústrias de bebidas e alimentos, os PLCs regulam máquinas de enchimento, controlando o volume exato de líquido em garrafas ou latas.
Máquinas de embalagem: Controlam o processo de embalagem, incluindo a selagem, etiquetagem e verificação de peso dos produtos.
3. Tratamento de água e esgoto
Estações de tratamento de água: Os PLCs monitoram e controlam os processos de tratamento de água, ajustando a adição de produtos químicos, gerenciando os sistemas de filtragem e monitorando os níveis de reservatórios.
Sistemas de bombeamento: Controlam bombas para a distribuição de água potável ou o bombeamento de águas residuais, otimizando o fluxo e reduzindo o consumo de energia.
4. Indústria Química e Farmacêutica
Controle de processos químicos: Gerenciam a mistura de reagentes, o controle de temperatura e pressão em reatores, e a destilação, garantindo a segurança e a eficiência dos processos.
Fabricação de medicamentos: Supervisionam ambientes estéreis e processos de fabricação de medicamentos, mantendo os padrões rigorosos de qualidade e segurança.
5. Energia e Utilidades
Subestações elétricas: Os PLCs controlam e monitoram subestações, gerenciando o fluxo de energia elétrica, a operação de disjuntores e a detecção de falhas na rede.
Sistemas de energia renovável: Automatizam a operação de parques eólicos e usinas solares, otimizando a produção de energia e monitorando o desempenho dos equipamentos.
6. Automação Predial
Sistemas de climatização (HVAC): Gerenciam sistemas de aquecimento, ventilação e ar-condicionado, ajustando a temperatura e a umidade para conforto e eficiência energética.
Controle de acesso e segurança: Automatizam portões, portas e sistemas de vigilância para garantir a segurança das instalações.
7. Transporte
Sistemas de sinalização ferroviária: Os PLCs são usados para controlar sinais e mudanças de trilho, garantindo a segurança e eficiência do transporte ferroviário.
Automação de aeroportos: Controlam sistemas de bagagens, pontes de embarque e iluminação de pistas, melhorando a operação e a experiência do usuário.
Perguntas Frequentes (FAQ)
O que é um PLC e como ele funciona na automação industrial?
PLC, ou Controlador Lógico Programável, é um tipo de computador robusto usado na automação industrial para controlar processos industriais e máquinas.
Ele monitora entradas e saídas para tomar decisões baseadas em um programa previamente definido pelo usuário, permitindo a automação de processos de fabricação, linhas de montagem e outras tarefas.
Como os sistemas elétricos são integrados com PLCs?
Os sistemas elétricos são integrados com PLCs por meio de entradas e saídas, tanto analógicas quanto digitais. As entradas recebem sinais de diversos sensores que monitoram condições como pressão, temperatura e fluxo, enquanto as saídas controlam atuadores, como motores, válvulas e relés.
A programação do PLC permite que ele processe esses sinais e execute comandos específicos para controlar os sistemas elétricos de forma eficiente.
Quais são os benefícios de usar PLCs na integração de sistemas elétricos?
Os benefícios incluem maior flexibilidade, precisão e eficiência na operação de sistemas elétricos. PLCs podem ser reprogramados conforme necessário, adaptando-se a novos processos sem a necessidade de alterar o hardware.
Eles também melhoram a segurança, pois podem ser projetados para reagir rapidamente a condições perigosas, e aumentam a eficiência operacional, reduzindo o desperdício e otimizando o consumo de energia.
Quais desafios podem surgir na integração de sistemas elétricos com PLCs?
Desafios podem incluir a complexidade da programação, a necessidade de compatibilidade entre diferentes dispositivos e sistemas, e a manutenção de sistemas integrados.
Também pode ser desafiador garantir a segurança e a confiabilidade dos sistemas, especialmente em ambientes industriais severos. Além disso, a atualização de sistemas antigos para integrar com PLCs modernos pode requerer um investimento significativo.
Como garantir uma integração bem-sucedida de sistemas elétricos com PLCs?
Para garantir uma integração bem-sucedida, é crucial planejar cuidadosamente e seguir as melhores práticas, incluindo:
Análise e planejamento: Entender as necessidades do sistema e planejar a integração detalhadamente.
Seleção de equipamentos: Escolher PLCs e outros componentes compatíveis com os requisitos do sistema.
Programação eficiente: Desenvolver uma programação clara e eficiente, seguindo padrões industriais.
Testes rigorosos: Realizar testes abrangentes em todas as etapas do processo de integração.
Treinamento e suporte: Providenciar treinamento adequado para os operadores e manter um suporte técnico eficaz.
A automação industrial vem se tornando uma parte integral do funcionamento das manufaturas, e a cada dia vemos mais e mais setores da economia automatizando seus processos.
Eletricistas e profissionais da área tem uma oportunidade grande nesse setor, e nós vamos te ajudar nisso.
Não deixe de comentar e compartilhar este artigo se te foi útil.
Veja também

Circuitos elétricos no quadro de distribuição: qual a forma adequada de distribuir?

Tipos de disjuntores: conheça as principais categorias!

Inversor de frequência: como controlar a velocidade de motores elétricos?

Sistemas de iluminação industrial: projeto passo a passo
Aviso legal
Todas as informações obtidas neste site e páginas de redes sociais relacionadas a ele são apenas de caráter INFORMATIVO. O Mundo da Elétrica NÃO se responsabiliza por nenhum dano ou prejuízo causado pela execução de ações relacionadas ou não ao conteúdo descrito aqui. Procure sempre um profissional qualificado, sigas as normas e utilize os equipamentos de proteção para qualquer trabalho que envolva eletricidade.